Find Out How Custom-Minted Coins are Produced
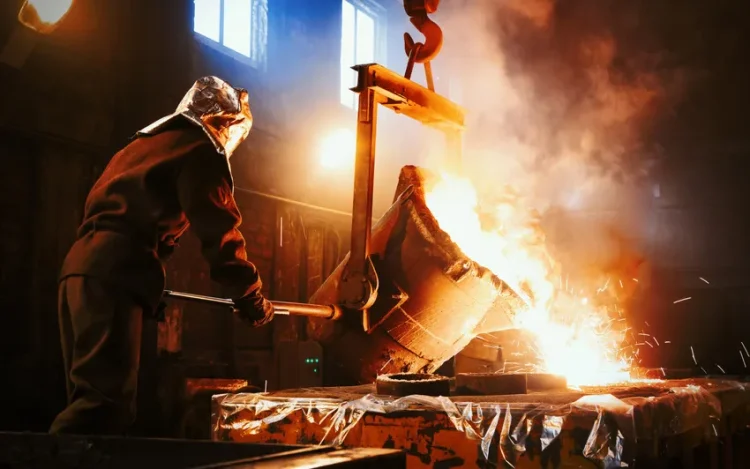
Have you ever wondered what path commemorative coins take before they go to the lucky owner? How exactly does a coin manufacturer bring custom-minted coins to perfection? Coin USA welcomes you to dive into the exciting guide on the production of custom-minted coins. Learn the secrets, ins, and outs of coin making below.
Crafting Coins: From Liquid Metal to Custom-Minted Coins in Beautiful Finishes
A coin stamping project always starts with the most important thing — the individual look that customers want their custom-minted coins to have . For this purpose, our coin designers work closely with the buyer and transform their idea into a personalized layout graphic , that illustrates how the final custom-minted coins will look like. This pattern is further modified and refined until, in the client’s opinion, it is perfect. Only then, the coin manufacturer handymen get down to work.
In our furnace, they melt the metal of our customer’s custom-minted coin project to its liquid state. The chosen alloy is then poured in lines of the correct thickness for the final coins. Only when the metal has cooled down and hardened, the coin manufacturer stamps out the coin rounds of the size our client determined for the project.
How the Pattern Is Applied to Custom Coins
In the meantime, several other very important steps have to be followed to put the individual design on the custom-minted coins. After the layout is approved, we prepare a production graphic that shows the relief of the custom-minted coins. Based on this second technical graphic, we make the minting tools:
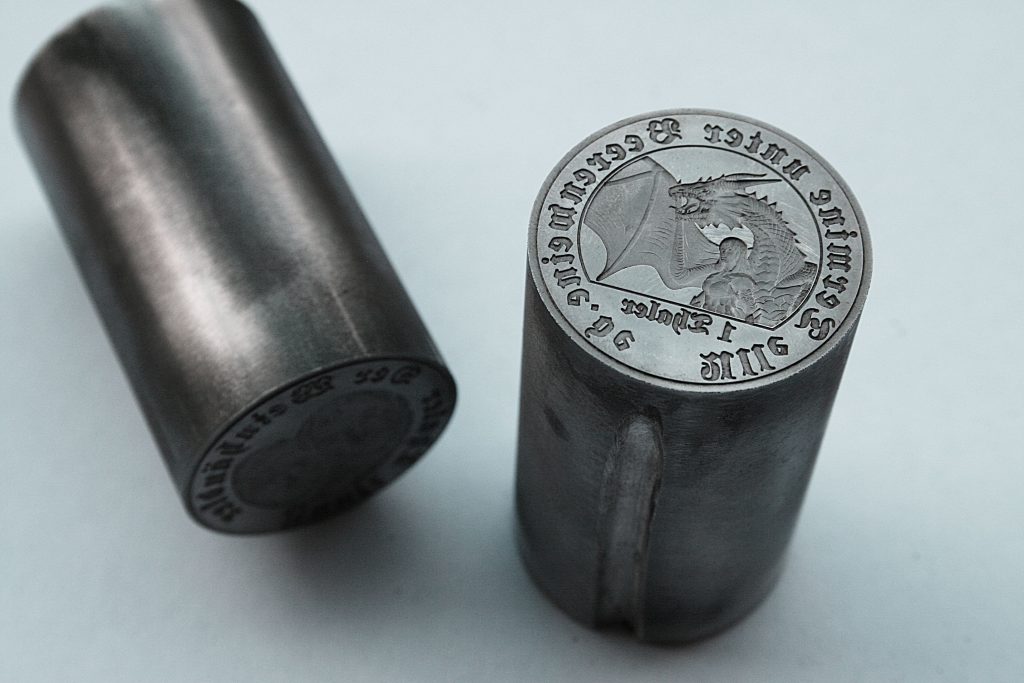
Firstly, a plasticine model much larger in size than the finished custom-minted coins is made, representing the base-relief to be achieved as in the endorsed set of graphics. This first plasticine model’s creation typically takes more than 2 weeks. Such a long period is due to the fact that the creator needs to consider a lot of nuances when completing the prototype of a clients’ custom-minted coins . The process is carefully supervised by the coin manufacturer.
The next step is to turn the big plasticine model into the real-sized rubber resin mold . The latter serves as a starting point in creating an epoxy resin mold for the production of custom-minted coins. Our coin manufacturing specialists put the epoxy mold on a pantograph, a squeezing device. This tool launches the exact outline of the mold onto a mill-cut master stamp made from resistant steel. This one, in turn, is already of the correct size for the final custom-minted coins.
Together with a matrix die, this master stamp serves as the basis for making another operating master die for our clients’ custom-minted coins. We also call it the master punch, reduced by the coin manufacturer’s special manipulation, until the needed master stamp for custom-minted coins is formed.
In today’s world, modern technology is an integral part of the traditional art of custom-minted coin production. So, a coin manufacturer ensures the creation of a custom-minted coin mold primarily by using computer-aided design (CAD) software .
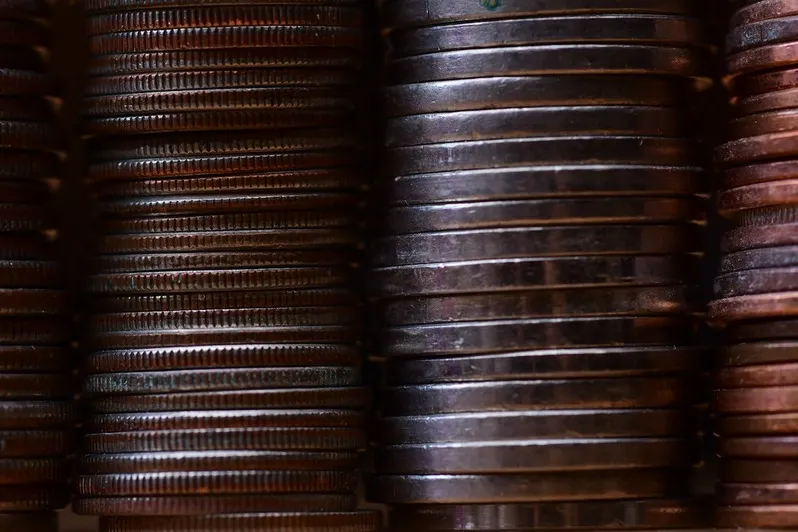
Coinage: It’s All About Pressure
Once the blanks are created, they must be properly hardened. To make custom-minted coins, hundreds of tons of pressure are applied to the prepared molds in order to shape the metal in between them. The manipulation can be repeated numerous times to ensure that the desired pattern is properly applied to the custom-minted coins.
It is important to be aware that most custom-minted coins have different designs on their front and back sides. This means that two different master stamps are designed. They are mounted on the stamping devices and then are fed into the loading hopper. In the actual stamping process, the blanks of custom-minted coins are subjected to pressures of up to 300 tons.
Plating and Colorization of Custom-Minted Coins
Once the custom-minted coins are made, the plating stage is set. Precious metals such as gold, silver, palladium, or platinum are typically used for this purpose. Precious metal-plated custom-minted coins are the result of a chemical process. It occurs as follows, the metal of which the custom-minted coins are stamped is added to a solution containing the precious metal with a synchronous electric current supply.
When customers wish for their custom-minted coins to be colorful, either hard or soft enamel color is applied to the correct emplacement on the commemorative coins, which are then heated. The heating is done by the coin manufacturer so that the custom-minted coins’ enamel paint dries and hardens in time. All necessary colors for this phase of custom-minted coins’ production are mixed by a special highly skilled craftsman
The conclusive step of custom-minted coins’ production is laser engraving of elements individual on each single coin.
-
The Thorough Final Inspection of Custom-Minted Coins
To make sure there are no technical errors, all custom-minted coins that leave our mint are thoroughly inspected. If there are any, our trained coin manufacturing technicians immediately correct them.
Would you like to have custom-minted coins of your own?
Try your hand in crafting the design of your future commemorative coins, using a Coin Configurator, right here on our website. Our team of creative coin designers and proficient coin manufacturers is eager to help you!
Disclaimer: Our products on this page are known as “Coins” in order to comply with general linguistic usage. It should be expressly pointed out that it concerns, however, individually embossed medals and no current or former means of payment/currency.